Become more environmentally conscious in your craft practice with this useful guide from the Green Crafts Initiative, including simple tips and advice on cutting down on waste, saving water and swapping your materials for more sustainable alternatives.
Together, Creative Carbon Scotland and Craft Scotland have created the Green Crafts Initiative, a sister project to the Green Arts Initiative. The Green Crafts Initiative is a nationwide accreditation scheme designed to provide Scottish-based makers and craft organisations with the advice, support and the tools they need to become greener. Learn more about the project and sign-up.
1. Collective buying sustainable materials
Often for makers, the biggest environmental impact of craft has already occurred at the point when one begins to work with the raw materials. As a result, choosing more eco-friendly materials, and working with more sustainable suppliers, is one of the biggest ways a maker can improve the sustainability of what they do.
However, sometimes sourcing more sustainable suppliers can incur a financial cost. Either in the time spent researching and experimenting with a new supplier, or in an increased cost in the material itself due to higher ethical or environmental standards.
To overcome this issue, it is possible to group together with other makers to either work with suppliers to leverage lower prices, or to take advantage of economy bulk purchasing.
Things to look for in a supplier
Sustainable alternatives to your materials will vary depending on your discipline, and there are a few things to consider. For example, in ceramics, the availability and sustainability of a certain type of clay. In jewellery you might need to consider whether the mined precious stones are certified as non-conflict sourced. Moreover, there are some things to examine when identifying whether a supplier is more sustainable than an alternative:
- Environmental policy: does the supplier have a positive stance on sustainability? Do they have a policy on their aims in this area? (normally in the About section, or the footer of supplier websites). Can you ask them about what they are doing to reduce their impact?
- Locality and seasonality: do they source in Scotland/the UK? Can they do so for particular products? Do they know what is seasonally appropriate for your needs?
- Toxicity: do they have a process for controlling any toxic waste created from their production processes?
- Social dimensions: do they support their local community? Are they a social enterprise?
- Carbon reduction initiatives: do they offer anything like carbon-neutral delivery?
How to organise
In order to seek and assess more sustainable (environmental and economic) buying options through a collective model, one needs to see what the available options are, and who would be likely to work with you. At a very simple scale, this could be working out who else buys from the same suppliers (is there a popular brand among your raw material suppliers?), or who else from your discipline is interested in investigating more sustainable options.
For example, collective purchasing to secure a better rate for energy supplies has been very popular in the past, and following a similar model on a studio or sector scale could be a good way to begin the process.
- Advertise: let others know you are looking into the sourcing of a particular material
- Register: get them to inform you of who their current suppliers are, what they are currently paying/using, and how much they tend to order on an annual/equivalent basis.
- Negotiate: talk to your selected suppliers about your sustainable materials option, using the leverage of the amount of business your collective may bring them.
- Switch: confirm and purchase the products at the agreed rate, and distribute to the new community.
Photography by Imani on Unsplash
2. Saving water in production
Water is one of our most crucial natural resources. However, due to the propensity for it to rain in Scotland, we Scots are notoriously bad at taking it for granted! Essential for human life and a huge range of domestic, industrial and craft purposes, our water supply needs a huge amount of movement and processing to make sure it’s suitable for our needs. Making the water industry one of the biggest users of energy in Scotland.
There are lots of ways individuals and studios can reduce their water consumption and increase their resource efficiency – and lots of reasons why they should.
Reasons to reduce your water usage
Saving money, building business resilience and reducing impact on the environment are the key reasons to reduce your water usage. More specifically, for those who pay business rates for water (domestic use is currently covered by Council Tax in Scotland), there are increasing costs around use and disposal, more pressure from government and regulators around safe water management, and more awareness of the carbon emissions impact of water use and its effect on climate change.
Ways to save water:
- Report leaks: even something as simple as a leaking tap wastes around 80 litres of water (enough to fill an average bath)
- Plug it: you can save two litres of water by using a plug in the sink when washing your hands
- Turn it off: only turning the water on intermittently when cleaning equipment saves around three litres of water
- Use it cold: use only cold water for cleaning floors or rinsing equipment
Getting started
Understand how you use water: considering how you use water in your processes and activities, where your biggest use of water is, and whether the water you use is heated/treated before you use it will give you a picture of your needs, and where you might be able to reduce your use.
Understand your bills: 90% Scottish organisations pay for their water and will receive a water bill. Comparing monthly or annual use, and understanding how this may correspond with your activity, will help you focus on cost reduction.
Consider new, efficient equipment: often new equipment can boost the efficiency of water use, offsetting the upfront cost of the equipment in a relatively short time frame. Organisations like Resource Effiency Scotland offer an interest free loan for new equipment that has resource efficiency savings (energy, water, waste). Some examples of such equipment might be:
- Tap aerators, which break up water flow into droplets for better wetting and reduced water use.
- A rainwater harvesting system for grey water use (e.g. toilets, cleaning).
Available funding for water-saving measures
The SME Loan fund, run by the Scottish Government, is available to SME's (small and medium-sized enterprises) based in Scotland. This loan can be used for energy, waste, water saving equipment and systems. Small to medium-sized businesses can borrow up to £100,000.
Get in touch directly with Resource Efficient Scotland by calling 0808 808 2268 to find out more about available funding, as grant and loan schemes change regularly, and their advisors can support organisations in completing their application forms.
For more support and ideas, visit:
Photography by Krys Alex on Unsplash
3. Sustainable ceramics
Ceramics are the oldest form of technology humanity has, from cooking and storing food, to preserving and telling stories. Porcelain, stoneware and earthenware are just some of the major types of potteryware produced by heating natural materials (often clay) to remove water for thousands of uses, with everything from crockery to jewellery.
As well as being a popular craft form in Scotland for individual makers, industrial ceramic production is also commonplace. Although the latter has more of a carbon footprint, this article focuses primarily on the choices and the changes makers can make to develop a more sustainable practice.
Source materials: origin, transport and locality
Beginning with the core input materials for any ceramic creation, interrogating the sources of clays and glazes is a good first step.
Clay
Clay is abundant in the world (some estimates indicate that everyone is no more than 200 miles from some clay), but it is still a finite resource that’s extraction produces much pollution and habitat degradation. Like other raw materials (such a metals), some varieties are more popular or more available than others, and makers should strive to source clays that are not so rare as to make their mining process damaging to the natural environment.
Similarly, sourcing clay more locally will reduce the carbon emissions and environmental impact of the international transportation of clays. Although gathering your own clay may not be suitable for everyone, working in collaboration with businesses like brickworks (who may allow you to reclaim their offcuts) or mining from the excavation waste of quarries could root your practice more locally in the near environment.
Finally, being mindful of the opportunities for working with reclaimed clay, past unfired projects, and using offcuts for the production of slip are all ways makers could reduce the raw material intensity of this input.
Glazes
There's a huge variety of glazes used by ceramicists in their work, each produce unique effects which are often central to each individual’s practice. Generally, makers should aim to use non-toxic, non-harmful colourants, and seek to use more naturally-derived dyes. In particular, avoiding any colourants that contain heavy metals (like lead) is a priority: waste materials often end up in waterways as a pollutant.
A note on salt glaze: in the past, salt glazes have been of particular environmental concern due to their production of an acid by-product. However, in the context of wider environmental impact, energy and transport emissions are much larger and more significant, and this should likely be where efforts in the sector are concentrated.
Processes: increasing efficiency
Once you have established greater sustainability in the materials you use, examining the form and efficiency of the firing process is a good next step.
Huge amounts of energy are required to heat a kiln to a suitable temperature, but it is possible to maximise the efficiency of that energy usage through a variety of methods.
Stacking and shelving
Makers already adjust how they form and stack kilns to achieve particular effects and finishes, but experimenting with the density of stacking can ensure that the kiln is being used as efficiently as possible. Generally, the higher the density of the stacking, the higher the temperature required; but sometimes lower temperature firings have to be extended in time due to the thickness of the clay, which in turn could make them less efficient. As every maker’s method (and kiln) is different, it’s best to try and monitor these variables to see how you can create the best effect with the lowest temperature and shortest time.
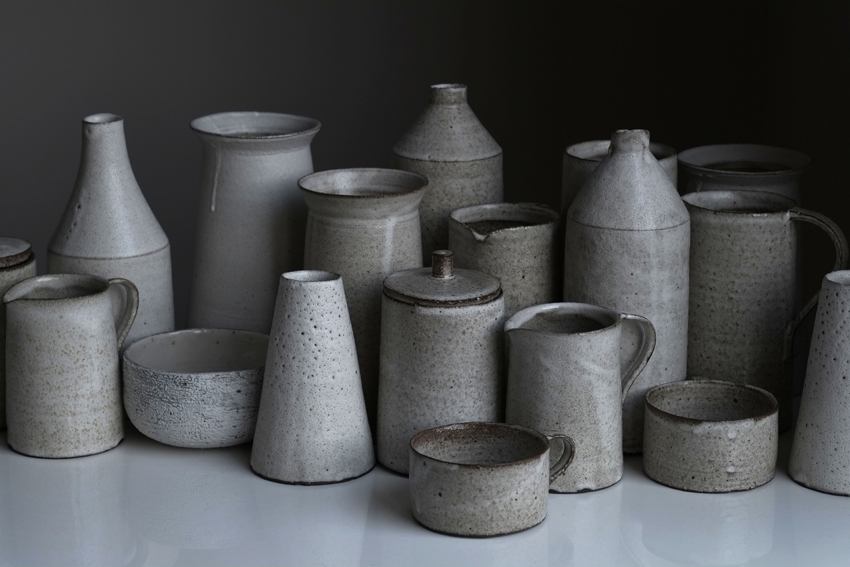
Photography by Tom Crew on Unsplash
Staggering kiln use
For those working in ceramic studios, one technique to reduce energy use is to stagger the uses of kilns throughout the day to better spread the energy use in the building. If all studio kilns are turned on at the same time, then it artificially inflates the demand for energy from the national grid, which in turn drives national energy production. This is most classically represented through the phenomenon of TV Pickup, a term used to refer to a phenomenon that affects electricity generation and transmission networks.
Similarly, in small studios, group firings might be possible: combining multiple kiln firings into a single event significantly increases the efficiency of the energy use.
Researching and adjusting your own kiln
Each kiln form (whether electric, wood etc.) will have a range of settings or methods of use to increase efficiency, and should be addressed on a case-by-case basis (through things like experimentation and manufacturers instructions – often the basic pre-programmed settings are not the most efficient).
- In many cases, wrapping kilns in ceramic fibre can massively improve their efficiency
- Adopting an industry-style firing time of around eight hours can also be a key way to reduce energy use by avoiding long pre-heats or overnight warm-ups
- Sometimes drying work with an electric fan, rather than using kiln re-heats, can be more efficient (depending on the kiln)
Sustainable and alternative fuels
Considering the energy supply to your kiln is also a way to make the firing process more sustainable. Changing your electricity supplier to a green tariff increases the demand and profile of renewable energy, and considering local materials when sourcing wood kindling or other fuel is a more sustainable approach. Recently the ability to use sustainably produced biodiesel or Waste Vegetable Oil (WVO – the kind produced by chip shops) in kilns instead of fossil fuels has created the opportunity to use biodegradable waste products for firing.
Ceramic waste: thinking creatively
Typically ceramics cannot be recycled through waste processing plants (household or industrial recycling). They can be downcycled (ground up and the powder used for slurry) but the result is often of a lower quality than the orginial. An alternative option is to creatively test if waste materials can be combined through a kiln casting process to form new materials (such as bricks, tiles, countertops). As well as being a potential income generation stream, this reduces the demand for virgin raw materials for these purposes.
Communications: talking about green ethos
One of the key ways makers can become more sustainable is by using their influence to reduce the environmental impact of their own practice, those they work with and that of their customers. Informing visitors to your website (or Craft Directory profile) of your sustainability ethos and actions is a key way to drive change. All makers in Scotland are also able to join the Green Crafts Initiative free of charge: a community of practice run by Craft Scotland and Creative Carbon Scotland that support and enables makers to reduce their environmental impact.
For more support and ideas, visit: